Recently, the first “National Outstanding Engineer” Commendation Conference has been held in the Great Hall of the People in Beijing. Dr. Xiong Dahe, the founder of SLon and inventor of the Slon VPHGMS, has won this award.
Dr. Xiong Dahe used forty years of persistence to innovate the design theory of strong magnetic separators, break through the bottleneck of its manufacturing, overcome the key technical problems of weak magnetic mineral separation, and independently develop the SLon series of strong magnetic separators. The machine has been used in large-scale industrial applications at home and abroad. The overall performance and technical and economic indicators of the equipment have reached the international leading level, which has enabled China to be in the world’s leading position in controlling the key technologies of super-large strong magnetic machines. It has greatly promoted the development of strong magnetic machines for weak magnetic mineral. The separation technology and equipment upgrades have greatly improved the utilization rate of low-grade weak magnetic mineral resources such as hematite, ilmenite, manganese ore, wolframite and rare earth ore, which reduces waste emissions and improves the utilization rate of strategic mineral resources. The self-sufficiency rate has made a significant contribution to ensuring national resource security and the healthy and sustainable development of the national economy, creating economic, social and ecological benefits exceeding 100 billion RMB.
In 1977, after Xiong Dahe was admitted to Jiangxi Metallurgical University to major in mineral processing engineering, he began to understand that the magnetic matrix of traditional magnetic separators was prone to clogging, and the separation of fine-grained weakly magnetic minerals had long troubled the mineral processing industry. From then on, he had the idea of studying vibration high gradient magnetic separation and embarked on the research path of “magnetic separation”.
When he was first assigned to the Ganzhou Nonferrous Metallurgical Research Institute in 1985, Xiong Dahe set the development of a new magnetic separator as his goal. After receiving the admission notice for a doctoral degree from Central South University of Technology, Xiong Dahe went to his supervisor and plucked up the courage to say: “I want to build a vertical ring pulsating high gradient magnetic separator that is unique in the world and can be patented. I will research it in the future. The rights belong to both the school and the institute, and the right to manufacture new products belongs exclusively to the institute. Can the institute support me?” The sincere eyes won the unanimous affirmation of the leaders of the institute. After Xiong Dahe proposed the plan and verified it, Ganzhou Nonferrous Metallurgical Research Institute allocated 100,000 RMB as funding for Xiong Dahe and arranged people to assist him in carrying out research.
He was taking classes while designing and processing. Finally, in 1987, the world’s first SLon-1000 VPHGMS designed by him came out! He pioneered the successful development of the SLon VPHGMS for mineral processing using a comprehensive force field that simultaneously utilizes pulsating fluid force, gravity and high gradient magnetic force. This magnetic separator innovates the vertical rotation of the sorting ring and the concentrate backsurging device. It is equipped with a pulsation mechanism to loosen the mineral particles and reduce the mechanical inclusion of non-magnetic mineral particles. Besides, it adopts a boat-shaped sorting area, a diversion method and other new technologies to achieve dynamic sealing of the slurry.
After 3052 hours of long-term application practice in Gushan Iron Mine, this equipment has been proven to completely overcome the machine clogging and mechanical inclusion phenomena of traditional high gradient magnetic separators, increasing the grade of iron concentrates by 6% and the recovery rate by 13%. The mineral processing index has created the highest level in the history of Gushan Iron Mine. Subsequently, he designed the expanded SLon-1500 VPHGMS, which can create economic benefits of more than 1 million RMB for Gushan Iron Mine every year.
In 2000, Anshan Iron and Steel Qidashan Ore Concentrator and Donganshan Sintering Plant originally adopted the gas reduction roasting and weak magnetic separation process, which consumed a lot of energy, cost, and caused serious pollution. The product quality could not meet the requirements. The industry faces the risk of transformation. After learning that Xiong Dahe’s latest design of the SLon VPHGMS was successfully applied in Gushan Iron Mine, Anshan Iron and Steel immediately invited Xiong Dahe to the site to guide the process transformation.
Xiong Dahe led the R&D team and a SLon-1500 VPHGMS to Anshan Iron and Steel Group Corporation, it was the severe winter season and the weather was extremely cold. Xiong Dahe was not afraid of the severe cold. Even if his hands are covered with frostbite, he still stayed by the machine every day. After three months of industrial testing, he finally designed and developed a new process from stage grinding to strong magnetic separation, and then to reverse flotation, successfully solving the problem of high energy consumption and serious pollution of the original process. After the process transformation, on-site production costs were significantly reduced, the iron concentrate grade increased by 3.83%, the tailings grade decreased by 3.15%, the recovery rate increased by 19.26%, and the iron concentrate grade exceeded the 67.5% mark, ranking first in the world. The new technology has enabled Anshan Iron and Steel Group Corporation to be selected into the “Guinness Book” of Chinese enterprises.
Since then, the SLon VPHGMS has become a star product in the mineral processing industry and has been used in major domestic mines for mineral separation, including various types of iron oxide ore, ilmenite, rare earth ore, non-metallic ore, and poor and weakly magnetic ores that are difficult to separate. More than one billion tons of ore are processed every year, creating the highest level in the history of China’s weakly magnetic iron ore, fine-grained ilmenite and various non-metallic ores.
For more than 40 years, the magnetic separation technology and equipment he researched have solved a series of engineering and technical problems for many metallurgical mines and non-metallic mines. More than 4,000 SLon series magnetic separators have been promoted and applied in more than 2,000 mines at home and abroad. The domestic market share of strong magnetic separators has reached more than 70%, with indirect economic benefits of hundreds of billions of RMB, and significant economic, social and ecological environmental benefits have been achieved.
With the successful promotion of SLon VPHGMS in China, Dr. Xiong Dahe and SLon magnetic separators have become increasingly famous internationally. He has been invited to South Africa many times to participate in international cooperative testing work. In view of the special characters of its ilmenite, Xiong Dahe designed the SLon Double Vertical Ring Pulsating High Gradient Magnetic Separator in accordance with international standards and exported it to South Africa in 1966, ending China’s long-term dependence on imports of strong magnetic equipment and creating a new era for China’s strong magnetic equipment exports.
In 2001, in response to the national call for the transformation of scientific research institutes to adapt to the new competitive environment and accelerate the transformation of scientific and technological achievements such as new technologies and products with internationally advanced levels, Dr. Xiong Dahe, with the strong support of superior authorities, based on the Equipment Research Laboratory of Ganzhou Nonferrous Metallurgy Research Institute, the state-owned and employee-owned SLon was established.
Xiong Dahe began to lead all the company’s personnel to seize development opportunities and aggressively enter the international market. So far, SLon magnetic separator series products have been exported to more than 30 countries such as the United States, Russia, and India, achieving an international market share of over 50% and making the overall level of China’s mineral processing equipment enter the world’s advanced ranks.
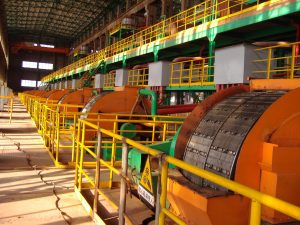
OLYMPUS DIGITAL CAMERA
Under the leadership of Dr. Xiong Dahe, the company has developed rapidly. SLon’s registered capital has increased from 5 million RMB at the beginning of its establishment to 150 million RMB, and state-owned assets have also increased more than 60 times in more than 20 years. The main economic indicators of SLon have maintained high growth for many years in a row, ranking first in the domestic and foreign strong magnetic separator markets. It has made outstanding contributions to the construction of China’s national economy in the fields of ferrous, non-ferrous and non-metallic mineral processing.
Up to now, Xiong Dahe has published more than 100 papers and written research reports at home and abroad, obtained 13 national patents (including 6 invention patents and 7 utility model patents), and won 1 second-class and third-class National Science and Technology Progress Award, 1 third prize for national invention, 1 national patent excellence award, 1 provincial and ministerial level special prize for scientific and technological progress, 6 first prizes, 4 second prizes, and 1 second prize for technological invention, as well as many honorary titles such as “National Expert with Outstanding Contribution” and “National Outstanding Scientific and Technological Worker”.
Xiong Dahe has spent his whole life pushing China’s weak magnetic ore beneficiation level to one commanding height after another. In his seventies, Dr. Xiong Dahe still adheres to the forefront of science and technology. Based on the original technology, he develops a high field magnetic separator. The background magnetic field is increased from 1.0T to 1.8T. He pioneers the frame modular yoke and sorting ring structure. The ultra-large SLon-5000 model has been developed. Compared with the original SLon-2000 model that is widely used, the processing capacity is increased from 80t/h to 950t/h, and the power consumption per ton of ore is reduced from 0.70kWh to 0.27kWh, saving 61% of electricity per ton. Mine water consumption drops from 2.08m3 to 1.19m3, saving 43% of water. A high recovery magnetic machine is invented, and the recovery rate of titanium operations increases from 58.4% to 85.2%. An aluminum alloy excitation coil magnetic machine is developed to reduce the cost of the entire machine by over 20%. It is precisely the breakthroughs in equipment and technology in the beneficiation of various weakly magnetic ores that have made this legend in the field of electromagnetic mineral processing.